The Dutch Institute for Basic Energy (DIFING) focuses on creating economic and social value from knowledge, leveraging research infrastructure to work with the industry to reduce risk and costs while advancing technology. It’s there.
As a well-known Dutch Institute, Differ has a prominent position in the innovation ecosystem. Courage is at the heart of the Institute’s strategy, focusing on co-evolution, technology transfer and spin-out.
“Courage creates value from knowledge by making it suitable and/or available for economic and/or social use, and converts it into products, services, processes, and entrepreneurial activities. It’s the process. “With that definition of the Netherlands Latenau Institute in mind, we’ll look at the courage to fusion. What is the difference, the Dutch Institute for Basic Energy Research, do you go to promote courage?
Large-scale science ecosystem
It is interesting to see the role of the Dutch NWO Institute in the large-scale science ecosystem. This applies to nikhef in basic particle and gravitational wave ecosystems with different fusion ecosystems, and space flight chambers and srons for space observation and instrumentation.
Typically, these large scientific institutions run their own scientific infrastructure and participate in the design, construction and exploitation of advanced equipment in international scientific infrastructure. For example, the difference is to analyze plasma-oriented materials and components for ITER and demos, to develop equipment and controllers for ASDEX upgrades, to develop TCVs in Germany, west France, or Switzerland. I’m involved. Additionally, Differenti has actively participated in activities such as Fusion4Energy’s Governance Committee, EuroFusion General Meeting, and the demonstration design team.
Push the boundary
The links between these activities and industry are very subtle. Companies benefit from participating in the design and construction of science infrastructure. This often encourages the expansion of technical capabilities that can be pursued in other markets. With the industry involved in large-scale, international scientific infrastructure, Geo-Return is often a long game with substantial upfront costs and significant risks.
However, what happens if you have your own internal research infrastructure, as different in the Netherlands? You can then make the industry involved in the design and realization of your infrastructure. This is a much less risky game, with significantly lower advance costs and a much greater chance of success. Science infrastructure, by almost definition, pushes the boundaries of requirements and complexity, and the Industrial Party develops the desired capabilities to promote technology. Pushing the boundaries of science infrastructure also drives the boundaries of industrial capacity, allowing industrial partners to acquire capabilities and develop new product lines.
Technology Transfer: When Magic Happens
In addition to joint development with Geo-Return, there will also be technology transfer. Technology transfer means that technology developed in a particular domain can be applied to another domain. The question is, what happened with the migration between these domains? This is often experienced as serendipity. Suddenly, there was insight, and suddenly, the opportunity was recognized. But maybe there’s a system to insanity and we can understand how we can move technology and how to encourage their development.
For successful technology transfers, you must start from the system level. Certain features are invested in inter-interfaced components to provide overall desirable behavior for a particular requirement. Technology forwarding requires functionality from artifacts in one domain, but typically works in additional functionality, different environments, different requirements, and different legal frameworks.
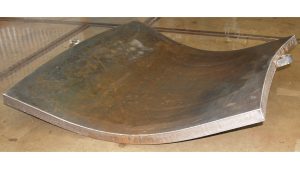
This means you need to work with new domain specialists to build something that works for a variety of purposes. Next are the market dimensions, such as knowledge creation, disclosure, evaluation and evaluation, IP protection, funding and technology development, marketing, commercialization, product development and impact. These are usually outside the realm of most scientists, and as a result, transfer of technology is often a difficult and dangerous effort.
Let’s highlight five examples of how different it can be in technology transfer. Create value from knowledge and push courage forward.
From Iter vacuum vessel to Airbus A380
The first example to be discussed is the formation of large metal crafts with complex shapes of Iter vacuum vessels. The Dutch company Exploform and Iter NL have invested in expanding the company’s capabilities to create artifacts of the right size. Ultimately, the company didn’t get a contract to produce an Iter vacuum vessel with new capabilities to form large-scale artifacts, but the company will produce a complex part of the Airbus 380 cockpit I was able to do that. Iter-NL helped eBloform to enhance its capabilities in large-scale science and instrumentation, and the company was ready to transfer this capability to new applications.
From nuclear fusion to care robotics
Another area is what we’ve worked closely with private companies in the past is what we’ve done in the past, remote maintenance. In a fusion reactor, blood vessel components become radioactive. As a result, once the machine is operated, it is not possible to access the systems and components within the blood vessels. Damage is inevitable due to the highly aggressive environment with high temperatures, plasma flux and extremely intense neutrons. These systems need to be maintained. But what do you think?
Robot maintenance of fusion devices is foreseen in the haptic master-slave system, a robotic system in which people mimic the movements and actions of manned operators. This is reminiscent of medical robotics.
At the time, hot cells were foreseen by ITER to maintain the large port plug. Build one complete virtual unit of hot cells. We have begun developing maintenance procedures for several equipment and have begun demonstrating that we can reach the subsystem (by plasma) that is most likely to break down. But you can also see how the entire team of four operators can work together. We studied the interfaces of human operators using robotics. We asked about understanding the tasks when multiple operators work on the same task, and asked whether the operator could be made concrete with computer-generated solutions via the haptics system.
Can the software identify problems such as collisions and obstacles? Can the software identify the appropriate sequence to support the operator? Logistics also plays a role. Can I track where the tool is? Can these tools be used in the following ways or are they considered useless? These topics can be explored from an integrated perspective.
Many of the aspects developed for advanced applications of ITER remote maintenance can be transferred to the care robotics system Rose (using TU/E and HIT) to assist in the care of elderly people. Care robotics should be inexpensive with relatively simple systems for simple tasks. These systems cannot handle more complex situations independently, but systems with over 100 remote operators can provide cost-effective robotics care.
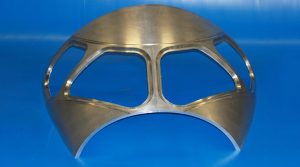
Prototype training simulator for heart surgery
The Delft University Faculty of Mechanical Engineering modeled the soft structure of a virtual environment and mimicked hoses and cables. These soft structural models are transferred to (simple) models of the heart, and become complicated enough to allow surgeons and medical students to train them to perform open heart surgery. In the virtual operations theater, young surgeons were able to pick up instruments such as scissors, scalpels, scalpels and mirrors to perform virtual open heart surgery. The project was carried out in close collaboration with healthcare professionals who gave detailed opinions.
Industrial inspection tool from Fusion Reactor, Life Science Diagnostic
Another example is the equipment developed with the Differ for the control of the so-called divertor. The bottom area of a fusion machine that we intentionally creates very cold plasma. In such cold plasma, radiation loss is induced, resulting in reduced heat flux to the first wall of the reactor. All this should be done under closed loop control.
We have developed a hyperimaging instrument for complete information on the radiating diverter state (in this particular case, in TCV Tokamak), consisting of spectral, spatial and temporal information. All cameras look at the same location of the diver through another filter (associated with a particular line radiation). The ratio between line radiation intensity represents the various processes that occur in diverters, and with these 10 cameras, the complete diverter state is controlled.
The system was developed by Wouter Vijvers, a former scientist at Differ. The contract as a project leader for ITER’s big instruments allowed him to work with half his time in the further development of his ideas. This set up the company’s chromodynamics, where the idea was launched for creating a high-tech hyperimaging microscope for cancer research. Afflicted tissues can already be identified at very early stages. What began as a fusion boosted medical research.
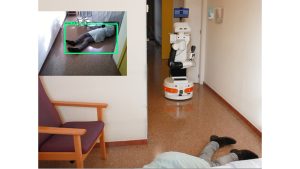
From fusion for advanced cancer treatment to fever control
The fifth example is a model prediction controller for current density and temperature distribution using local microwaves. The TU/E team demonstrated the controller at the Swiss TCV. The controller allows for simultaneous control of current density distribution and total plasma pressure, taking into account the limitations and constraints. This controller can be forwarded by the same researchers to the application of hyperthermia therapy, a cancer drug treatment developed by Phillips.
At high temperatures, drug therapy (such as in cancer) that needs to be deployed in specific tissues is effectively preserved in nanocapsules. At normal body temperature, the nanocapsules are closed. Locally depositing microwave beams within the body allows the tissues where the drug needs to be deployed to high temperatures. The nanocapsules are opened and the drug is deployed to locally attack the cancer. Model Prediction Controller (MPC) was originally developed for the Fusion domain, but was ported to Philips Medical from Differ and Tu/E.
future
In many ways, we work with private parties on many projects to stimulate the process of courage. I believe in long-term relationships across different projects and research groups.
Co-development as a way to achieve knowledge transfer during the early design stages makes it more compatible with industry requirements and needs. This applies to fusion research and chemical energy and nuclear fission.
This article will also be featured in the 21st edition of Quarterly Publication.
Source link