With unparalleled HTS expertise and decades of R&D lineage, the HTS-110 helps fusion innovators navigate the challenges of high-field magnets and compress development timelines.
The world has changed, and so has fusion changed. Commercial fusion was once an exclusive territory of large government programs such as ITER and the National Institute. However, the landscape has changed over the past decade. Over half of new fusion projects leverage magnetic confinement (such as Tokamaks, Stellarators, or other concepts), and a significant share of these efforts has identified robust, high-field magnet systems as their top priority . This transformation coincides with global electrification, rising venture investments and the urgency of climate targets. In short, the world has changed and high temperature superconducting (HTS) magnet technology has become the center of the short-term viability of fusion.
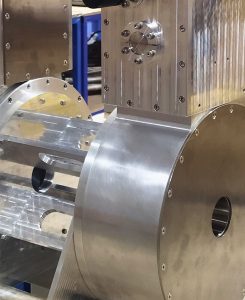
The HTS-1010 was not originally created to provide this fusion boom. Rather, we have evolved from pioneering research in New Zealand. This concerns copper plate superconductors containing Bi-2223, the material that supports first-generation high-temperature superconducting tapes. The founding team, which spun out in 2004, addressed the challenges of advanced industrial and beamlines, providing lightweight generators, mine sweeper coils and magnet systems for X-ray or neutron scattering. These early deployments proved that HTS is superior to laboratory prototypes and can provide a stable field without liquid helium. However, when fusion developers began to seek stronger, more temperature-resistant magnets for 10-20 Tesla operations, we found ourselves on the frontline. itself.
Origins, early industrial developments, and commercial fusion entries
The HTS-10 backstory tracks the former Ministry of Science and Industry Research (DSIR). So Dr. Bob Buckley and Jeff Taron identified the BI-2223 structure, leading to commercial production of HTS tapes. By 2007, the Berlin electron synchrotron, one of the first cryogenic HTS magnets in the X-ray beamline, was fed with a 5-Tesla split pair solenoid, followed by a 5-Tesla split pair for Australian nuclei. Ta. Science and Technology Organization (ANSTO). We have deep-built practical HTS expertise that combines electromagnetic modeling, crystat integration and mechanical enhancement through homopole motor coils, custom magnet prototypes, and energy storage applications.
When next-generation fusion developers realized the possibility of HTS reaching higher fields at temperatures more accessible than LTS, they needed a magnet that could be magnified while still maintaining reliability. Our proven track record naturally extends into this new domain, leveraging the same user-centric, in-house approach, but adapts to Fusion’s higher field targets and larger production requirements.
Dealing with Quench Protection and Thermal Stability
A key concern, particularly in superconducting magnets, is quenching. In low-temperature superconductors (LTS), quench propagation speeds are relatively high. If the magnet is properly designed, the energy deposition spreads quickly throughout the coil and can withstand such events. In contrast, HTS exhibits low quench propagation velocity. Local transition to a resistive state risks depositing energy in small areas that can irreparably damage the coil.
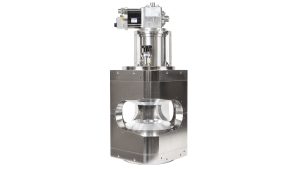
Fortunately, HTS conductors have extremely high thermal stability, are much less likely to quench under normal conditions, and can detect developing quenches and shut down magnets before damage occurs. It will be more sexual. The HTS-110 has embedded continuous monitoring – coil temperature and voltage monitoring – within the magnet design to ensure that operation remains within a safe envelope. This synergistic effect of low quench likelihood and robust detection can be applied to advanced fusion magnets where conserved energy can be immeasurable and reliability is of paramount importance.
A brief note on the appeal of helium and HTS
HT often eliminates or reduces the use of helium by operating at higher temperatures (20-30 K, not ~4 k), but some magnets may be due to partial cooling or initial cooldown It relies on helium. With the global market facing helium shortage 4.0 and associated cost instability, cryogenic or helium optical systems are becoming increasingly attractive. Our Designs Integrate CryoSaver™ leads (dramatically reduce conduction losses) and robust cryogenic people combine to mitigate helium supply risks and simplify on-site operations.
Core R&D: 4 integrated product lines for fusion
Much of the HTS-110’s ability to meet commercially available fusion needs comes from in-house R&D, which refines coil winding, conductor qualifications, cryogenic integration and fast debilitating magnets. Over time, it has become a four-integrated product line that crystallizes these learnings and helps new fusion entrants skip years of trial and error.
SuperCurrent™ – Wire Quality Control
Many QA processes rely on LN2 (~77k) in fields near zero, and defects associated with ~20k and 10~20t, typically when many fusion magnets need to operate Or hide your actions. Supercurrent was developed by the Robinson Research Institute to measure critical currents (ICs) under realistic conditions. When used by groups such as wire makers and Commonwealth Fusion Systems, large wire batches meet strict specifications and reduce the risk of coil failure.
cryosaver™ – efficient current leads
Transferring current to a cryogenic environment can waste energy and complicate cooling. Cryosaver Leads – employed in over 2,000 installations worldwide – reduce conduction losses by up to 90%, ease refrigeration demand, and accelerate commissioning of both fusion and industrial magnets. With a rating of 150 A to 3 ka or higher, it makes it versatile in a variety of applications.
Custom-made HTS coil: cryoforge™
At the center of every magnet there is a stable coil, which will improve mechanical reinforcement, quench protection and coil geometry. The results: a family of coil modules that currently accommodate non-planar or complex shapes, as well as standard circular and racetrack designs. Currently, we are focusing on compact and efficient coils for prototypes, but future expansions may cause these modules to be scaled towards larger fusion magnets in the concept of advanced reactors.
Fast ramping and high field approach
Some magnets need to rapidly circulate between different magnetic fields. The 7 T Moke (Magneto-optic Kerr Effect) magnet completes a 4-quadrant ramp in under 60 seconds with continuous duty cycle, indicating the suitability of the HTS for rapid field changes. These magnets are widely adopted in industrial development and qualifications for new data recording media where high field capacity, high throughput, and high reliability are essential requirements. The development of a rapid stop magnet relied on important studies conducted in the HTS-10 to understand, predict and manage electrical losses within the cycle of the HTS coil. The central solenoid of the large tokamak cycles even faster (+25t to -25t in ~10 seconds), but the experience of fast broken magnets is important without matching with the extreme demand for solenoids. Control or compensation coils can be notified.
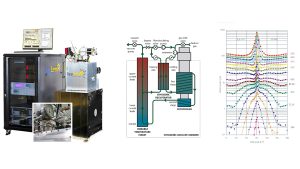
We will adopt Rebco, the next-generation magnet
Early HTS tapes relied on BI-2223, which was essential for early commercial magnets. However, modern fusion designs are turning increasingly to REBCO (rare earth barium oxide) due to their high in-field current density, excellent mechanical strength, and excellent performance, which has a high ability to operate at high temperatures. Several manufacturers around the world are expanding REBCO production to meet the surge in demand, making it the next cost-competitive option for the waves of fusion coils. The HTS-110 incorporates REBCO tape into a design that requires higher field thresholds and smaller coil footprints, focusing on robust and manufacturing solutions for advanced reactors.
The HTS-1010 does not operate the SuperCurrent™ platform in-house, but works closely with wire suppliers. This synergy allows for seamless integration of REBCO or BI-2223 tapes, allowing you to adjust the coil design as new conductor variations emerge. By incorporating real-world wire performance insights, maintaining a close-knit project timeline without sacrificing reliability. This is a key factor in building magnets in Fusion’s demanding performance envelopes.
Beyond the first plasma: Scaling commercial fusions
All fusion magnets pose unique challenges in geometry, temperature margins, and mechanical strengthening. The HTS-110 addresses this front with a systematic end-to-end approach starting with a detailed design study covering electromagnetic fields, thermal modeling and quench protection, proceeding through coil windings, assembly and rigorous verification. Masu. Over the years, it has proven its capabilities by supplying beamlines, homopole motors, and magnets for neutron scattering. I understand how to scale my prototype into a consistent, repeatable system. For commercial fusion, it is all converted under one roof, into a single point of responsibility for design, manufacturing and testing, balanced with the efficiency of a standardized product line.
If you need high field magnets, advanced coil modules, or simply expert guidance, we recommend working with us. Please contact us today. Find out how our in-house R&D, engineering depth, and proven commercial delivery can support your fusion roadmap, from initial demonstrations to net energy. Together, we can quickly track Fusion’s future on a global scale.
reference
Commonwealth Fusion & SuperCurrent: MIT DSPACE Publication. NM Strickland et al. , “Applied Superonuctivity, vol. 31, no. 5, pp. 1-5, August 2021, Art No. 9000305, doi: 10.1109/tasc.2021.3060355. Fusion Industry Association https://www.fusionindustrusterassociation.orgHigh-temperature conductivity Linear critical current database https://htsdb.wimbush.eu Robinson Research Institute https://robinson.ac.nz/
This article will also be featured in the 21st edition of Quarterly Publication.
Source link