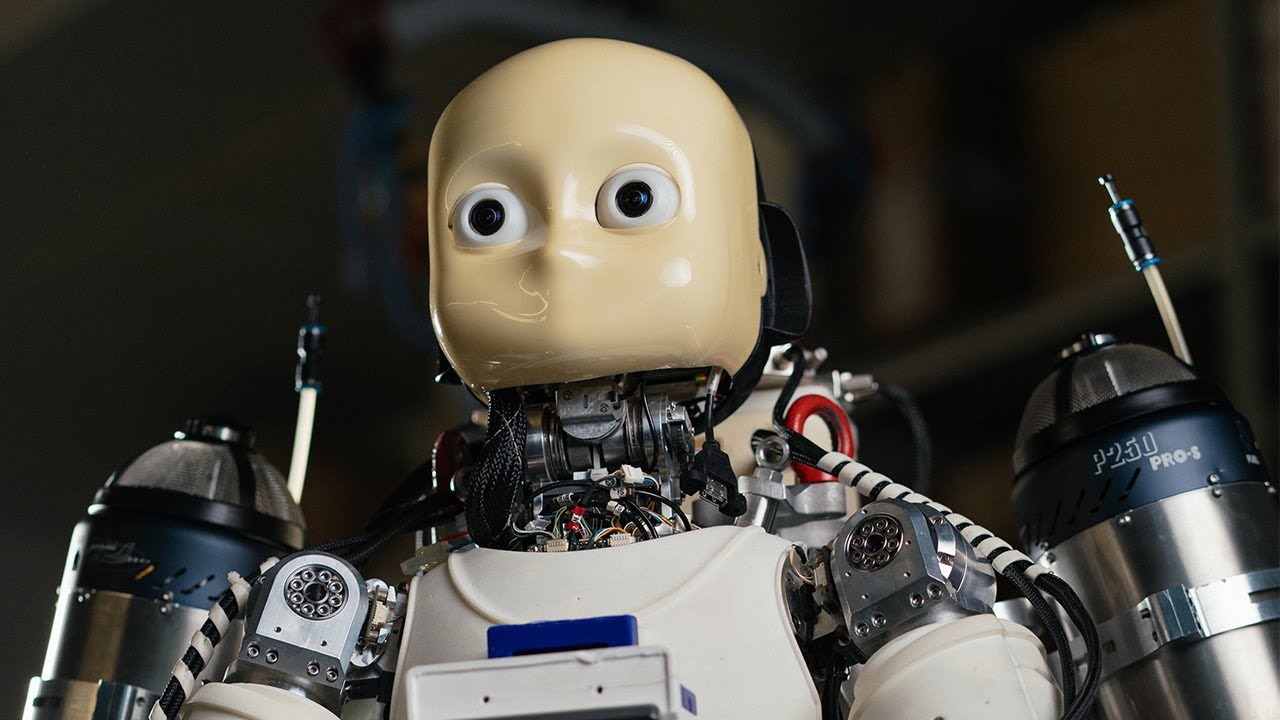
Please take a look
Researchers demonstrated the first successful vertical lift-off of humanoid robots. This is a major step towards flying robots that mimic human abilities.
A new robot called the IronCub Mk3 uses four thrusters to achieve vertical thrust, two being integrated into the arm and two being attached to the back.
In the footage released on YouTube on June 18th from the Italian Institute of Technology (IIT), Mask Doning’s robot is held from the suspenders and then activated, using a thruster to lift approximately 20 inches (50 cm) off the ground.
You might like it
ICUB robots based on IIT humanoids seem to be kid-like in both size and appearance. Weighing 49 pounds (22 kilograms), it measures 3 feet (1 meter) tall while adopting a childlike dimension and adopting a very recognizable smooth and shiny “baby face” head.
First launched in 2009 by the RobotCub Consortium of European universities, this is designed as a testbed for the research of human cognition and artificial intelligence (AI) and has been used in countless projects over the past 16 years.
In a corresponding study describing the robot released on June 1st on the ARXIV preprint server, IIT engineers say that the expanded version of the robot is the first jet-driven flying humanoid robot designed to take off. They added that the work highlights the new possibilities that humanoid robots will fly and present.
Related: Robots: Facts about machines that humans can walk, talk, and perform tasks that humans can’t (or don’t)
In contrast to many other robotic platforms currently under development, the focus is usually solely on ground-based movement and manipulation, but adding air mobility provides support for search teams and rescue missions, allowing them to cross collapsed buildings, flooded areas, or other terrain that humans cannot access.
This type of robot can combine its ability to interact with its environment with flight to help remove debris and find or extract victims.
The authors of this study also point out that repairs can be performed on structures that are difficult for humans to access, such as underneath the bridge. They can even deploy in dangerous environments where people cannot operate safely, such as nuclear leaks or chemical leaks.
The world’s first jetpack-powered flying robot
IronCub is based on IIT’s ICUB3 platform. The system is designed to emulate many human abilities as the robot is remotely controlled by an operator wearing head-up displays (HUDs) like virtual reality (VR) helmets and other specialized equipment.
To equip the ICUB for flight, the team added loading mounting brackets to secure the jetpack and the new titanium spine that supports its weight. Previous versions of IronCub have problems igniting the thruster exhaust, so heat-resistant panels and covers have been added to the ICUB chassis. The thruster tilt angle was also adjusted to help with stability during flight and to keep the exhaust away from the robot’s body.
In this version, the robot’s forearm and hand removed to create space for the thruster attached to the arm, but the team says that the forearm is still fully compatible and read in later iterations.
To allow the chassis to handle takeoff and flight stress, the team performed finite element method (FEM) analysis. This is a problem-solving technique that focuses on decompositioning the structure into smaller interconnect components. As a result, they applied axial load of 750 Newtons (three times the peak thrust of each turbine) to the brackets of the jet engine.
One of the main challenges of achieving flight with this type of humanoid robot is to occupy all the joints and actuation points, adjust them, adjust and adjust the thrusters, so the robot will not fly on course or upside down.
Engineers managed this with what is called linear parameters called Changed Model Predictive Control (MPC), a complex flight controller that constantly calculates optimal joint positions and jet throttle.
Scientists then first extensively tested the system in computer simulations before beginning actual testing due to the safety risks of operating thrusters with exhaust temperatures above 1,112 degrees Fahrenheit (600 degrees Celsius).
After successfully demonstrating the launch with predefined trajectories and accurate tracking, the team is currently planning to focus on improving the flight controller to handle external obstacles that may occur during real flight scenarios such as wind and other bad weather.
Source link